The #1 HVAC design myth: low CapEx is better.
Controlling the climate is a top concern for indoor farmers, both in controllability and operating costs. It should be since climate is largely responsible for crop health and avoiding crop losses.
HVAC (Heating, Ventilation, and Air Conditioning) systems are the best way to maintain ideal growing conditions to help optimize yields and minimize losses.
But sadly, HVAC costs are often underestimated due to lack of understanding or oversight.
Many farmers think they can piece a system together themselves or draw simple quotes from online catalogs or home improvement stores.
HVAC is a complex system that has to be fitted to each farm’s needs, each farmer’s desires, and the constraints of the situation.
Explore the constraints of your system with this worksheet.
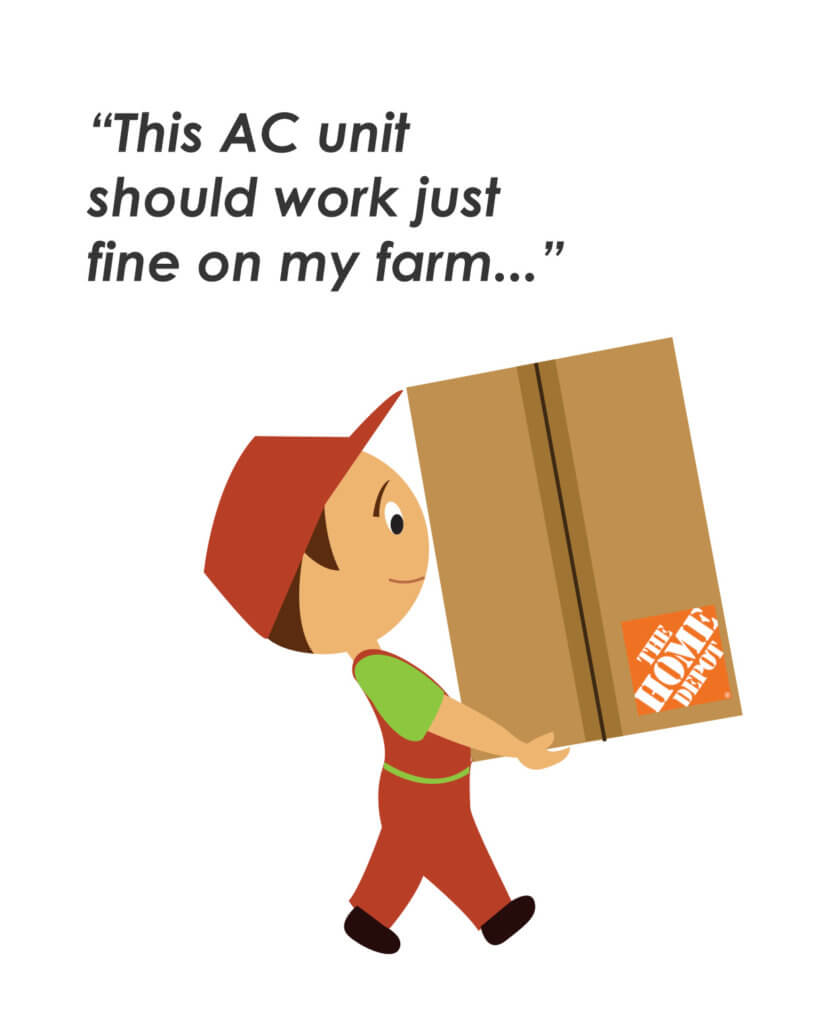
For commercial farms, an off-the-shelf system can cost more in the long run than a properly fitted system.
When farmers underestimate HVAC, they get themselves into a bind with investors and limit the production of the farm in the long run.
The majority of this underestimation comes from the myth that farmers can choose cheaper options without a significant impact on operating cost.
Surveys conducted by Dr. Nadia Sabeh, Founder of Doctor Greenhouse, show that most farmers budget 50% of their energy and maintenance (i.e. OpEx) costs for HVAC, but only budget 5–10% of their equipment costs (CapEx) on HVAC.
These expectations reflect a flawed assumption.
In reality, farmers who invest in a properly sized HVAC system on the front end can reduce the ongoing costs of operating their farm and increase yield.
This ends up being a worthwhile investment for any indoor farmer, whether growing in a greenhouse, warehouse, or container farm.
Take Farmer Hank.
Hank planned $6,000 for his HVAC equipment in his farm, and he presented that estimate to investors.
After spending a few hours online and on the phone getting quotes, however, CapEx started to cast a bigger shadow.
All the numbers he got from manufacturers and contractors landed around $50,000. Hank had only budgeted one-tenth of that cost!
That budget of $6,000 had already been presented to and approved by Hank’s investors. Now what?
Luckily, Hank had a mentor to help him find the resources and info he needed to find a middle ground between HVAC needs and investor expectations. Working with a consultant, Hank estimated a second option: a fitted, higher-quality HVAC system that would cost him $12,000.
This type of oversight can get farmers like Hank into trouble. To avoid Hank’s situation, plan realistically for HVAC, and don’t be afraid to get help from an engineer or contractor!
Dig deeper: discover your constraints and needs with a worksheet.
What happens when a farmer invests more capital?
HVAC only takes 5–10% of CapEx budget. Right?
Wrong.
Hank didn’t understand that to lower OpEx, he needed a correctly sized HVAC system that would seamlessly handle the heating, cooling, and humidity for his farm.
That meant raising CapEx. Although this meant a few thousand dollars more on the front end, it would start saving him money after a few years.
For instance, let’s compare two scenarios.
In Scenario A, Hank gets an off-the-shelf HVAC system that isn’t quite sized right for his operation.
This costs him $6,000.
In Scenario B, Hank spends the extra money to get a professionally sized HVAC system.
This costs him $12,000.
At first glance, the OpEx (energy costs and maintenance) for the off-the-shelf system (A) isn’t that much higher…
A) Off-the-Shelf operating costs = $4000/yr
B) Right-Sized operating costs = $3500/yr
That’s only a 12.5% difference. Hank’s thinking, “Not bad for saving $6,000!”
Then Hank starts thinking about the bump in revenue that Scenario B could get him. Improved temperature and relative humidity control mean higher yields, more weight, and fewer crop losses.
With Scenario B, Hank could get a 20% increase in sellable product and a 10% decrease in crop losses.
On top of better yield, Hank can steer crops towards higher quality, better chemical profile, and a more predictable (consistent!) product. Hank’s product is looking better and better to his markets, which can count on him for volume and quality.
After all this, Hank’s price premium has increased 20%, earning him an additional $1,200 per year.
It takes Hank 3 years to make up the additional $6,000 he spent on a properly sized HVAC system.
Want to benefit from Scenario B?
While Scenario B was more difficult to arrange with investors, it ended up being much more economical in the end. Hank was able to use the numbers projected by his consultant to convince his investors that a quality HVAC system would be better for both his farm and their investment.
Get access to our HVAC design webinar below and figure out how much of your CapEx you should budget to HVAC.
In this webinar, Dr. Nadia Sabeh from Doctor Greenhouse will explain and dispel other HVAC design myths, like:
- HVAC can be accomplished with an A/C unit from Home Depot.
- I can build this system without an engineer or contractor.
- HVAC is just a heater and cooler.
- HVAC makes my location and climate irrelevant.
- HVAC functions the same regardless of facility type.
Farmers can skip Hank’s confusion by preparing for HVAC with a professional.
You can get instant access to the equivalent of an hour of professional consulting for just $10 through the “Keeping It Cool: HVAC Design Considerations for Growing Indoors” webinar. (Check it out here. Free for Upstart University students.)
Dr. Nadia Sabeh is founder of Doctor Greenhouse and a mechanical-agricultural engineer with nearly a decade experience designing HVAC systems with farmers.
Her expertise in plant-environment relationships, including the effects of light, temperature, humidity, and nutrient levels on plant responses allows her to identify the right HVAC solution for growing lettuce, tomatoes, strawberries, cannabis, and even alternative proteins.
Dr. Nadia is more than familiar with Hank’s situation and has helped countless indoor growers start and run impressive greenhouses.
what size HVAC unit for a 358sqr ft. greenhouse it has a3 ft r15 skirt is 228 sq ft,the rest is covered 8ml plastic in and out plus polyethylene wave panels i estimate it to have 2320cubic ft we will install a electric 2000 wat heater we would like to use it year around winters are 30 minus celcius some times average -12 summer is the opposite average15 plus with 30 plus high the size is 22×16 10 to the ridge advise would be much appreciated fred.
is hvac the way to go it wil also have 2 12inch eqhaust with temp control and 2 12inch motorized air intake